What’s on the outside matters too.
Key Takeaways: What You will Learn About Pharmaceutical Packaging
- ► There are 3 types of pharmaceutical packaging: Primary, Secondary and Tertiary.
- ► Materials for pharma packaging can vary but they are all intended to protect the integrity of the size and chemical makeup of the drug.
- ► Vision inspection is an all-in-one solution for advanced pharma packaging defect and anomaly detection.
- ► Newer technologies like A.I. and machine learning are making significant changes to the entire medical industry.
Outside of the medical field it is easy to take the “small stuff” for granted. In most countries, people are fortunate enough to have the ability to bring a prescription to a pharmacy and get the medicine they need. This is a very straightforward transaction. Typically, you get the prescription, read the label, tear into that box/bottle/vial, and feel better in a few days. While it may seem easy-peasy, there were plenty of unseen obstacles coming between you and that medicine.Types of Pharmaceutical Packaging
Pharmaceutical Primary Packaging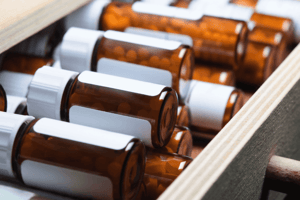
Any material that comes in direct contact with the product. This has very stringent requirements and methods for inspection. There are plenty of options here including vials, bottles, pouches, syringes, stoppers, blister packs, etc.
These products can vary for medical device packaging.
Pharmaceutical Secondary Packaging
Additional packaging that will contain the important medication information, like the ingredients and instructions, but never touches the product itself. A good example would be the box holding the blister pack.
Pharmaceutical Tertiary Packaging
This packaging is invisible to the end-user and protects the goods during the shipping process. It is essentially packaging to protect the packaging.
Which Materials are Used in Pharmaceutical Packaging
Pharmaceutical packaging relies on a particular range of materials designed to protect product integrity and comply with strict regulatory compliance standards. Common materials for primary packaging include glass which is still often used for vials, plastics like polyethylene and polypropylene, which are lightweight and durable and aluminum which is frequently used for its barrier properties against moisture, light, and oxygen. All material is selected based on the drug’s sensitivity to environmental factors, required shelf life, and mode of administration. This ensures that the packaging not only protects the product but also supports safe and effective delivery to patients.
Materials like Tyvek®, High-Density Polyethylene (HDPE), Low-Density Polyethylene (LDPE), Polyethylene Terephthalate (PET) and Polyvinyl Chloride (PVC) are commonly used for medical device packaging as well.
How Pharmaceutical Packaging can go Wrong: Common Risks
Think of the containers, receptacles, and distribution devices as the final line of protection. They ensure:
-
- Contamination does not enter the medication/human body.
- The contents will not be altered.
- The required dose will be administered.
- The individual handling the medication is protected and can do so safely.
Material Imperfections
It is not simply the material that houses the vaccine or medicine that can affect the make-up of the fluid but the state of it. Before vials can be filled, the glass and stoppers/crimps/plungers must be 100% inspected for dust, foreign particles, dents, scratches, cracks, defects, discoloration, and shape perfection. Any of these factors can affect the integrity of the pharmaceutical and impede a person’s health.
Quite frankly, the consequences of poor pharma packaging are life threatening. The medicine is one thing but getting it to the user is another. To begin with, the material of the primary packaging can change the chemical makeup of the drug/vaccine simply through touch. This is why there was a potential risk of a supply shortage for the distribution of the COVID-19 vaccine. Without knowing the chemical makeup of the vaccine, manufacturers were unable to purchase materials without running the risk of them being a hazard.
Once the materials are selected, they must be perfect. Often, primary packaging must be 100% coated in a distinct substance to protect the contents from any interaction with the plastic, glass or rubber. If there is a single scratch, dent or bubble in this coating, it compromises the medication. In addition to the unwanted material canoodling, parts of that coating can mix into the medication as well.
Foreign Substances
Another example of unwanted material is what may lay on the receptacle itself. As with any recipe, a variation to the ingredients of pharmaceuticals will alter the end-result. Therefore, it is crucial to inspect all primary packaging for dust, fingerprints, grease or other foreign substances, including molecules invisible to the human eye.
Measurements, Size and Shape
In certain cases, the size and shape of the container must meet the exact design specification as the filling and labelling of the receptacles are automated for speed and accuracy. While on an assembly line, any inaccuracies may result in incorrect dosages.
The same logic applies to the stopper of the container, whether it is plunged or capped. The shape and size must fit exactly to prevent leakage and protects the users who manipulate it.
Labelling & Proper Identification
All packaging must be labelled correctly prior to distribution. If mis-labelled, the medication becomes both useless and dangerous. This is the vital information that will contain everything the user needs to know and is equally as important as the medication itself. This applies to all 3 types of pharma packaging. These goods cannot be released without confirmation of its contents.
One Solution to Rule them All: Automated Vision Inspection
The good news is that all these issues can be address by a single technology. Visual inspection systems have the capacity to verify and detect the smallest inconsistency and are commonly used in medical device testing. There are several benefits to automated medical packaging inspection including high-speeds, the removal of subjectivity, risk reduction and higher return on investment.
Automated test equipment is revolutionizing the industry because it is so thorough. The system itself can be designed to fully control and automate the lighting, temperature, and other environmental factors. As a result, inspection location becomes more flexible. Once a system is designed, the metrics can be manipulated based on the product under inspection. With this data, the same equipment can be leveraged for multiple product types with minor tweaks to the hardware.
Using vision software, limits and requirements are set automatically and the system can run independently with zero operator intervention. In addition, inspection results are automatically logged and organized for increased traceability to support compliance requirements and insight into the product. Naturally, this must be done using a standardized delivery process to assure consistent quality. The right system will also provide a full validation & documentation package to simplify the IQ/OQ/PQ process.
Serialization and Track & Trace
Serialization is the process of assigning a unique identifier like a serial number to each saleable unit. It is tracked throughout the supply chain, enabling full traceability from manufacturer to patient delivery.
This is crucial to avoid counterfeiting, which is a global issue in the pharmaceutical industry. By making each product traceable, it becomes significantly harder to enter the supply chain undetected. Serialization is also a significant component to remain compliant with most countries’ regulations, as it is used to ensure product authenticity and safety.
Combined with track & trace systems, it empowers stakeholders to verify product origin, movement, and destination, which at the end of the day, protects patients. Manufacturers can easily monitor inventory, manage recalls efficiently, and improve supply chain transparency.
Emerging Technologies in Pharmaceutical Inspection
As pharmaceutical production becomes more complex and quality standards more stringent, innovative technologies are transforming how defects are detected, and packaging is validated.
Machine Learning and AI for Defect Detection
AI-powered inspection systems are revolutionizing defect detection by identifying subtle anomalies that the human eye alone would certainly miss. These technologies adapt to product variations, improving overall accuracy. Machine learning also enables predictive maintenance and process optimization, which helps manufacturers prevent defects before they happen.
Hyperspectral and Infrared Imaging
Hyperspectral and infrared imaging go beyond regular light to detect chemical composition, contamination, and inconsistencies in pharmaceuticals and packaging. These are especially valuable for inspecting products, where internal defects or foreign substances may not be visible to the naked eye.
3D Vision and OCR/OCV for Label Verification
3D vision systems provide depth perception, allowing for precise inspection of packaging, fill levels, and CCIT / seal integrity. When combined with Optical Character Recognition (OCR) and Optical Character Verification (OCV), they ensure that printed information like batch numbers, expiry dates, and barcodes is both present and accurate.
Why Averna for Packaging Line Vision Inspection
When it comes to pharmaceutical packaging, perfection and compliance are non-negotiable. Averna delivers advanced vision inspection solutions tailored to the unique demands of pharmaceutical production lines. From detecting defects to verifying labels with OCR/OCV, Averna’s systems combine high-speed imaging with smart software so every unit meets quality standards. Their test engineering expertise allows manufacturers to catch issues early, reduce waste, and maintain full traceability.
Errors in pharmaceutical packaging can trigger recalls and damage trust. With Averna’s packaging line automation expertise, manufacturers improve quality and protect their investment. Contact us to discuss your inspection challenges
--
You may also be interested in…
Are you thinking about test instead of new product development? BPO may be the answer.
Get in touch with our experts or navigate through our resource center.